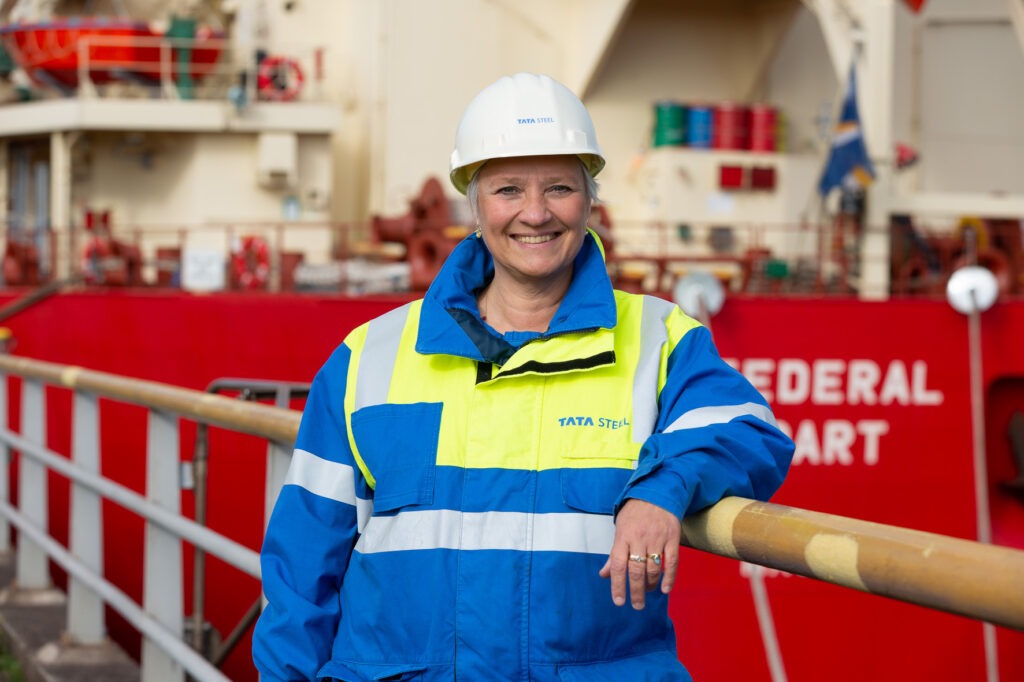
Langs parallelle routes naar een energieneutrale staalproductie
Tata Steel in IJmuiden produceert jaarlijks zo’n zeven miljoen ton staal. De staalproducent probeert dat zo duurzaam mogelijk te doen. De twee belangrijkste aspecten daarin zijn de circulariteit van het product staal en het verminderen van de CO2-uitstoot.
“In 2050 hopen we energieneutraal staal te kunnen maken.”
Zo efficiënt mogelijk met je energie omgaan is onlosmakelijk verbonden met de staalproductie, waar de marges altijd onder druk staan en de component energie in de prijs groot is. Sinds 1990 is de hoeveelheid energie die nodig is voor het maken van een ton staal met meer dan dertig procent gedaald. IJmuiden is een van de energiezuinigste staalfabrieken ter wereld.
Energie besparen en zo duurzaam mogelijk produceren zijn dus geen nieuwe onderwerpen bij Tata Steel, vertelt Annemarie Manger, directeur Sustainability & HSEQ. “Daar zijn we al heel lang mee bezig. Het is natuurlijk wel zo dat het nog nadrukkelijker op de agenda is gekomen, dankzij het Klimaatakkoord. Maar ook doordat mogelijkheden om duurzamer te werken, toenemen.”
Het artikel in NVDO Vakblad Asset Management
Vier miljoen ton CO2 minder
“De klimaatdoelstellingen van Parijs lijken ver weg, maar 2030 begint voor ons morgen al vanwege de benodigde modificaties aan de assets. Over tien jaar willen we vier miljoen ton CO2 minder uitstoten per jaar, dat is ongeveer een derde van de totale CO2-reductie die aan de industrie is opgelegd. Verder weg, in 2050, hebben we de ambitie om CO2-neutraal staal te kunnen maken, hopelijk op basis van waterstof.” Waterstof maken kost heel veel elektriciteit en dat doe je idealiter met groene energie. Daarom is waterstof iets voor na 2040, legt Manger uit. “De beschikbaarheid van voldoende windenergie vanaf de Noordzee is bijvoorbeeld belangrijk hiervoor.”
100 megawatt-waterstoffabriek
Ondertussen werkt Tata Steel samen met chemiebedrijf Nouryon en de Port of Amsterdam aan het H2ermes-project, een 100 megawatt-waterstoffabriek op het terrein in IJmuiden. Bedoeling is om met groene energie tot 15.000 ton waterstof per jaar te maken. De fabriek moet over vier jaar operationeel zijn en energie leveren voor duurzame staalproductie, en aldus zorgen voor minder CO2-uitstoot. De waterstof moet ook beschikbaar komen voor gebruikers in de regio, bijvoorbeeld voor emissievrij openbaar vervoer en transport en verwarming van gebouwen. Dankzij deze fabriek wordt er nu al gewerkt aan een distributienetwerk voor waterstof voor de Metropool Regio Amsterdam.
Korte termijn
Voor de middellange termijn zet Tata Steel in op het afvangen en opslaan van CO2 in lege gasvelden onder de Noordzee, het zogenoemde CCS: Carbon Capture Storage. Met EBN (Energie Beheer Nederland) inventariseert Tata Steel welke gasvelden in aanmerking komen. Samen met Gasunie en Port of Amsterdam onderzoekt Tata Steel de mogelijkheden om het bestaande leidingnetwerk te gebruiken, zodat er een CO2-netwerk ontstaat in het Noordzeekanaalgebied waarop partijen CO2 kunnen afleveren of afnemen. “CO2 opslaan in lege gasvelden is breed geaccepteerd als oplossing in dit geval. Want het gaat hier over lege gasvelden in zee. Het wordt wereldwijd toegepast en er is bewijs dat het werkt.” Op de wat langere termijn komt CCU in beeld: Carbon Capture and Usage. Hierbij worden hoogwaardige restgassen uit het productieproces opgevangen en zodanig bewerkt dat ze kunnen dienen als grondstof voor de glastuinbouw of chemische industrie.
Duurzamere maaktechnologie
In IJmuiden is de afgelopen jaren hard gewerkt aan een nieuwe, duurzamere technologie voor het maken van staal. Deze nieuwe technologie, HIsarna, vraagt minder energie en de CO2-uitstoot neemt met ten minste twintig procent af. “Dat is zonder afvang. Met afvang loopt het op tot tachtig procent.” HIsarna bestaat uit een reactor waar bovenin ijzererts wordt ingevoerd. Het erts wordt bij een hoge temperatuur vloeibaar gemaakt in een cycloon en druppelt op de bodem van de reactor waar steenkoolpoeder wordt geïnjecteerd. Het koolpoeder reageert met de gesmolten erts, waarbij vloeibaar ruwijzer ontstaat als basismateriaal voor de productie van hoogwaardig staal. Het gas dat HIsarna uitstoot, is geconcentreerd CO2. De technologie maakt een aantal voorbewerkingsstappen overbodig en stelt minder strikte eisen aan de kwaliteit van de grondstoffen. Dit resulteert in een enorme efficiëntieverhoging. Het verlaagt het energieverbruik, dringt de CO2-uitstoot terug met twintig procent en verlaagt de uitstoot van fijnstof, zwaveldioxide en stikstofdioxide met ten minste zestig procent.
Proeffabriek
In IJmuiden staat nu een proefinstallatie met een capaciteit van 60.000 ton. Op termijn moet er een commerciële HIsarna-fabriek komen in IJmuiden. “We zitten midden in het leerproces, ook voor onderhoud. Alles gebeurt in een cycloon en dat zorgt voor heel andere productie-omstandigheden en een ander slijtageproces. Traditioneel heb je een sinter- en pelletfabriek nodig als tussenprocessen, met heel veel slijtage en hun eigen CO2-uitstoot. Dat wordt totaal anders.” Het proefproject loopt nu ruim vier jaar en er worden constant nieuwe proeven gedaan om het proces nog energiezuiniger te krijgen. “Staal van auto’s kun je moeilijk hergebruiken omdat het verzinkt is. HIsarna kan het zink wel scheiden, waardoor we het auto-staal kunnen gebruiken. Dat is pure winst.”
Circulariteit
Staal is van nature honderd procent recyclebaar. Het staal dat bijvoorbeeld na demontage van gebouwen en bouwwerken vrijkomt, wordt nagenoeg volledig gerecycled. Staal is ook herbruikbaar: op een gelijkwaardig of hoger niveau dan het oorspronkelijk gebruik. “Klanten vinden het ook steeds belangrijker. Ze willen weten hoe wij onze CO2-uitstoot terugbrengen en hoeveel staal we recyclen. Sommige afnemers willen zelfs een duurzaamheidsaudit uitvoeren, wat prima is want daar leren we van.”
Grondstoffenverbruik terugdringen
“Erts blijft nodig, maar de grondstof is al heel circulair. Er gaan weinig materialen verloren tijdens het productieproces en dat nog verder optimaliseren heeft constant onze aandacht. De gassen die ontstaan tijdens de staalproductie gebruiken we voor energieopwekking en daardoor zijn we nagenoeg zelfvoorzienend qua energiebehoefte. Van de restproducten die ontstaan tijdens productie gaat 99 procent terug het proces in. We kijken continu naar onze producten om te zien of het duurzamer kan. Dat doen we met zogenoemde Life Cycle Analysis, een tool waarmee we vaststellen hoe duurzaam het productieproces is van nieuwe productontwikkelingen. Blijkbaar doen we iets goed, want hiervoor ontvingen we een Steelie Award van de Worldsteel Association.”
Blikfabriek
Verpakkingsstaal (blik) en duurzaamheid liggen dicht bij elkaar, zegt Manger. Tata Steel ontwierp en bouwde een nieuwe fabriek waar duurzaam staal wordt verbonden met een polymeer, zodat de blikken in één productiegang gemaakt worden en de traditionele tussenstappen niet meer nodig zijn. “Energiezuiniger, veiliger en een schoner productieproces.” Met Dow Chemicals werkt de staalproducent in een pilot aan een manier om CO en CO2 om te zetten in grondstoffen voor de chemische industrie.
Parallelle route
“Het opschalen van een nieuwe technologie is niet eenvoudig. Daarom lopen we parallel een andere route met CCS, dat wel een bewezen technologie is. CCU biedt vervolgens allerlei opties om nuttige producten te maken. Met World Class Maintenance werken we aan duurzame onderhoudsconcepten in Fieldlab Techport Smart Maintenance. De ambitie is om onderhoud honderd procent voorspelbaar te maken, wat bijdraagt aan een lager energieverbruik en daarmee aan onze duurzaamheidsdoelstellingen.”
“We werken veel samen met andere industriepartijen en met de overheid. Het energie- en CO2-vraagstuk overstijgt de behoefte van één bedrijf. Er is nationale infrastructuur nodig voor een waterstofnet, bijvoorbeeld. Je moet ook goed kijken hoe je elektriciteit overal veilig en betrouwbaar krijgt. En ook de businesscase moet kloppen. Door corona lijkt er vertraging te ontstaan in de uitvoering van de Europese Green Deal, maar wij gaan door met onze plannen. Helderheid is daarbij wel gewenst.”
Puzzelen met corona
“Ik ben nu ruim een half jaar actief in deze functie. Het was een ‘zachte landing’ omdat ik vanuit engineering al betrokken was bij CO2-reductie. In eerste instantie dacht ik ‘duurzaamheid, veiligheid, milieu en kwaliteit; dat gezondheidsdossier zal wel meevallen’. En toen kwam Covid-19. Alle kantoormedewerkers werken nu vanuit huis, maar onderhoud en productie gaat grotendeels door. Direct vanaf het begin van de coronacrisis hebben we lopen puzzelen: wat kan op afstand, wat kan slimmer. Houden we kantines open, welke extra persoonlijke beschermingsmiddelen zijn nodig? We zorgen ervoor dat tijdens werkzaamheden de anderhalvemeterregel in acht wordt genomen, we plaatsen schermen waar dat kan en nodig is. Als iets door twee man binnen anderhalve meter moet worden uitgevoerd, dan zorgen we voor de juiste persoonlijke beschermingsmiddelen. Bepaalde onderhoudstaken zijn daarnaast uitgesteld, bijvoorbeeld omdat de Italiaanse leverancier niet kon komen. Ik ben supertrots op de flexibiliteit van onze mensen in de fabrieken die de boel draaiende houden én op de thuiswerkers die in een hele nieuwe dynamiek blijven werken aan alle verbeteringen in onze processen.”
Geef een reactie
Je moet ingelogd zijn om een reactie te geven.