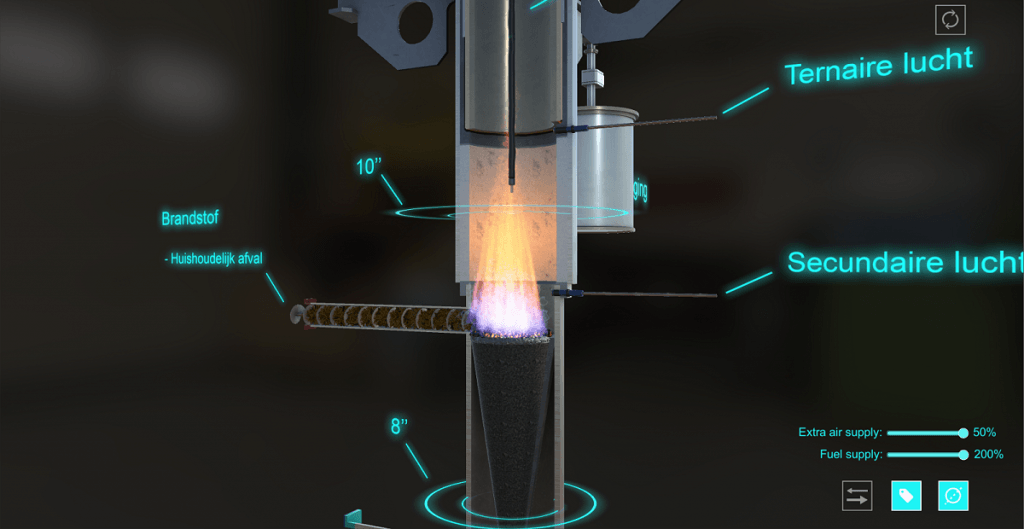
Vuurvaste bekleding in afvalverbrandingsovens vertoont soms onverwachte schades. Waarschijnlijk omdat ‘het vuurvast’ te heet wordt door het verbranden van onbekende chemische stoffen in het afval. Voorspelbaar maken van het onderhoud door betere proceskennis moet uitkomst bieden. In het project de Lerende Steen werken diverse partijen daarvoor samen.
Gouda Vuurvast is initiatiefnemer van het innovatieproject De Lerende Steen. Het bedrijf ontwikkelt, produceert en installeert de vuurvaste materialen.
Kan het beter?
“Wij zijn marktleider in de waste-to-energy markt in Nederland en lopen al lang rond in deze sector. We constateerden dat veel parameters in het verbrandingsproces onbekend zijn. We vroegen ons af of dat niet anders en beter kon”, zegt directeur Arie van Vliet. “Maar wat heb je daarvoor nodig?” Uit onderzoek bleek al snel dat een gedegen aanpak zeker in de miljoenen euro’s zou lopen. “De vraag werd vervolgens: wie kunnen ons daarbij helpen?” Er werd een subsidiefonds gevonden (EFRO), Energieonderzoek Centrum Nederland (ECN) werd partner en onderwijspartijen, Hogeschool Amsterdam, Vakwijs en Galileo sloten zich aan. iTZiT is de IT-partner en WCM de penvoerder.
Iedere afvalverbrandingsinstallatie is anders
Het lastige met de vuilverbrandingsinstallaties (avi) is dat iedere situatie anders is. De ene avi is de andere niet en zelfs binnen een avi kan de situatie per ketel verschillend zijn. Dat komt door de verschillende soorten afval en de samenstelling ervan. De avi’s verbranden huishoudelijk afval, bedrijfsafval, chemisch afval en afval dat afkomstig is uit het buitenland. “Maar je weet nooit de exacte samenstelling en als je al een ruw idee hebt, dan kan het per ‘grijper’ ook nog eens flink verschillend zijn. De oorzaak van de schade aan het vuurvast (beton, stenen en tegels) is meestal dus niet duidelijk”, zegt projectleider Mark Scheltes.
Real time simuleren
De eerste stap in de Lerende Steen is het meten van de werkelijke procesomstandigheden, zoals temperatuur, gassamenstelling en reducerend en oxyderend verbranden. ECN doet die meetcampagnes bij verschillende avi’s en zal vervolgens de resultaten ervan simuleren in een proefopstelling die nu wordt ontwikkeld. Scheltes: “Als we de verbrandingsomstandigheden real time kunnen simuleren dan kunnen we de faalmechanismen in de ketels ook vaststellen. Bvendien kunnen we dan ook onze productontwikkeling erop afstemmen.”
Eerste resultaat
De temperatuurmetingen leverden al een eerste – onverwacht – resultaat op. De ankers waarmee het vuurvast is bevestigd is, worden namelijk warmer dan verwacht. Scheltes: “Waardoor je in een andere corrosiezone zit dan je op basis van je warmtedoorgangsmodel zou verwachten. De vraag is dus: kan die temperatuur naar beneden, of hebben we een ander materiaal nodig voor het anker?”
Sensoren zoeken
De metingen die ECN nu doet, gebeuren over een periode van een of twee weken. “Maar eigenlijk wil je dat continu doen. Dus moet je sensoren zoeken of ontwikkelen, want je zit met die hele hoge temperaturen. We kijken naar sensoren die van buiten de ketel met licht of geluid kunnen meten wat er binnen gebeurt. Als je real time kunt meten, kan je een grote stap zetten. En als je vervolgens het faalmechanisme weet dan kan je het proces beter sturen en krijg je een onderhoudsvriendelijke situatie. Honderd procentvoorspelbaar onderhoud is een mooi streven. De vuilverbranders zijn in ieder geval enthousiast.”
Simulatiemodel
Scheltes: “We willen kunnen aantonen dat er verbanden zijn tussen wat de avi’s verbranden en de reacties van het vuurvast. Dat moet leiden tot een simulatiemodel waarmee we het verbrandingsproces beter kunnen besturen en waarmee je kunt voorspellen wanneer welke schades optreden. Dat is beter dan alleen andere vuurvaste materialen blijven proberen om het vuurvast verder te optimaliseren, want dat blijft vechten tegen de bierkaai.”
Integrale aanpak
“Of dit project uniek is? Ja, er wordt elders ook wel gemeten, maar voor zover ik weet nooit integraal, nooit het hele proces. Het gaat dan altijd om een specifiek probleem, bijvoorbeeld corrosie door chlorides. Hiervoor wordt dan een oplossing gezocht en vervolgens gaat men door naar het volgende probleem. Dat willen wij anders doen.”
Onderwijs
Mensen moeten ook leren hoe het simulatiemodel straks werkt. “Smart maintenance wordt sowieso steeds belangrijker. Daarom doet het onderwijs ook mee. Zij kunnen de ervaringen uit het project vertalen naar het curriculum en lesmodules.”
De reden om het innovatieproject te doen is duidelijk, besluit Van Vliet. “Het levert een voorsprong op in de markt. Betere producten, een procesoptimalisatietool voor in de controlekamer en lagere onderhoudskosten.”
De Lerende Steen wordt mede mogelijk gemaakt door:
Geef een reactie
Je moet ingelogd zijn om een reactie te geven.